What is Porosity in Welding: Key Elements and Their Effect On Weld High Quality
What is Porosity in Welding: Key Elements and Their Effect On Weld High Quality
Blog Article
The Science Behind Porosity: A Comprehensive Guide for Welders and Fabricators
Recognizing the detailed systems behind porosity in welding is essential for welders and fabricators making every effort for remarkable craftsmanship. From the structure of the base materials to the intricacies of the welding procedure itself, a multitude of variables conspire to either worsen or alleviate the existence of porosity.
Comprehending Porosity in Welding
FIRST SENTENCE:
Examination of porosity in welding discloses essential understandings into the stability and quality of the weld joint. Porosity, defined by the presence of tooth cavities or voids within the weld steel, is a common worry in welding processes. These voids, otherwise effectively addressed, can jeopardize the architectural stability and mechanical residential or commercial properties of the weld, resulting in prospective failings in the finished item.
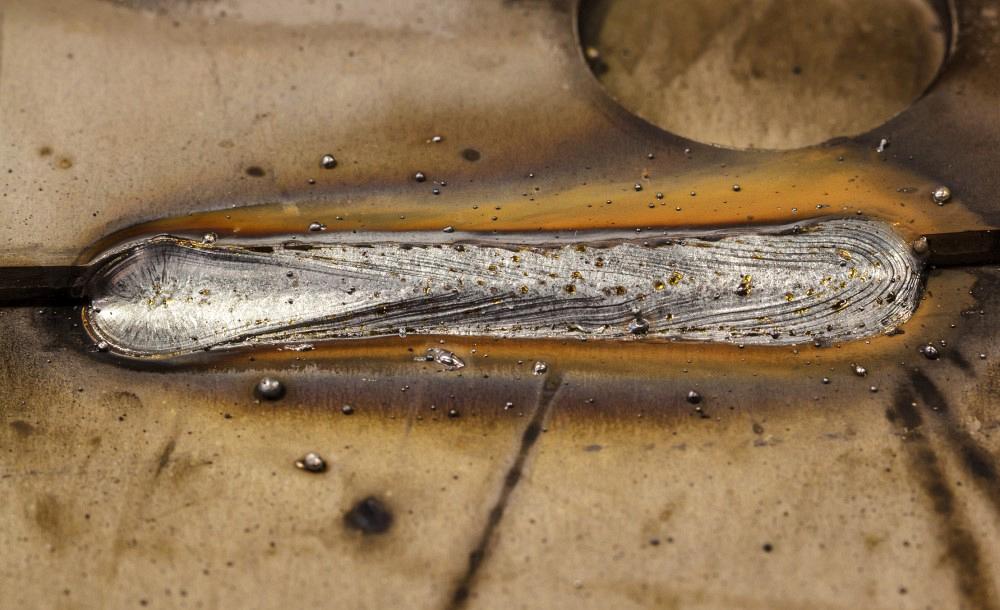
To discover and quantify porosity, non-destructive testing methods such as ultrasonic testing or X-ray evaluation are frequently used. These techniques enable the recognition of inner issues without jeopardizing the integrity of the weld. By analyzing the size, shape, and distribution of porosity within a weld, welders can make informed choices to boost their welding procedures and accomplish sounder weld joints.

Variables Affecting Porosity Development
The event of porosity in welding is influenced by a myriad of aspects, ranging from gas securing efficiency to the intricacies of welding criterion settings. Welding specifications, consisting of voltage, current, travel rate, and electrode kind, also effect porosity development. The welding technique employed, such as gas steel arc welding (GMAW) or secured metal arc welding (SMAW), can influence porosity development due to variants in warm circulation and gas coverage - What is Porosity.
Impacts of Porosity on Weld Quality
The visibility of porosity also damages the weld's resistance to rust, as the trapped air or gases within the voids can react with the surrounding environment, leading to destruction over time. In addition, porosity can impede the weld's capability to withstand stress or influence, more jeopardizing the general high quality and dependability of the welded framework. In important applications such as aerospace, vehicle, or structural building and constructions, where safety and toughness are paramount, the destructive effects of porosity on weld top quality can have extreme repercussions, stressing the significance of decreasing porosity via correct welding methods and procedures.
Methods to Minimize Porosity
In addition, using the appropriate welding criteria, such as the correct voltage, existing, and travel speed, is vital in avoiding porosity. Preserving a consistent arc size and angle throughout welding also assists minimize the chance of porosity.

Moreover, choosing the right protecting gas and preserving appropriate gas circulation rates are vital in lessening porosity. Utilizing the appropriate welding technique, such as back-stepping or using a weaving movement, can likewise aid disperse heat uniformly and lower the opportunities of porosity development. Guaranteeing proper ventilation in the welding environment to remove any potential sources of contamination is essential for accomplishing porosity-free welds. By applying these strategies, welders check here can effectively decrease porosity and create high-grade bonded joints.
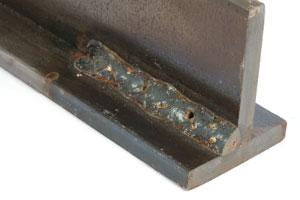
Advanced Solutions for Porosity Control
Executing innovative technologies and cutting-edge techniques plays a pivotal duty in accomplishing superior control over porosity in welding procedures. One sophisticated solution is the usage of sophisticated gas combinations. Protecting gases like helium or a mixture of argon and hydrogen can help in reducing porosity by offering far better arc stability and boosted gas insurance coverage. Additionally, employing sophisticated welding strategies such as pulsed MIG welding or modified ambience welding can also help mitigate porosity problems.
Another sophisticated solution involves making use of sophisticated welding equipment. Utilizing tools with integrated features like waveform control and innovative power sources can improve weld top quality and decrease porosity dangers. In addition, the execution of automated welding systems with specific control over criteria can significantly decrease porosity defects.
Furthermore, incorporating advanced surveillance and inspection technologies such as real-time X-ray imaging or automated ultrasonic screening can help in finding porosity early see in the welding process, permitting immediate restorative actions. Overall, incorporating these innovative remedies can substantially enhance porosity control and enhance the overall quality of bonded parts.
Verdict
In verdict, comprehending the science behind porosity in welding is vital for welders and fabricators to create top quality welds. investigate this site By identifying the factors influencing porosity formation and implementing methods to lessen it, welders can improve the total weld high quality. Advanced services for porosity control can further enhance the welding process and ensure a strong and dependable weld. It is necessary for welders to continuously enlighten themselves on porosity and execute best practices to accomplish optimal results.
Report this page